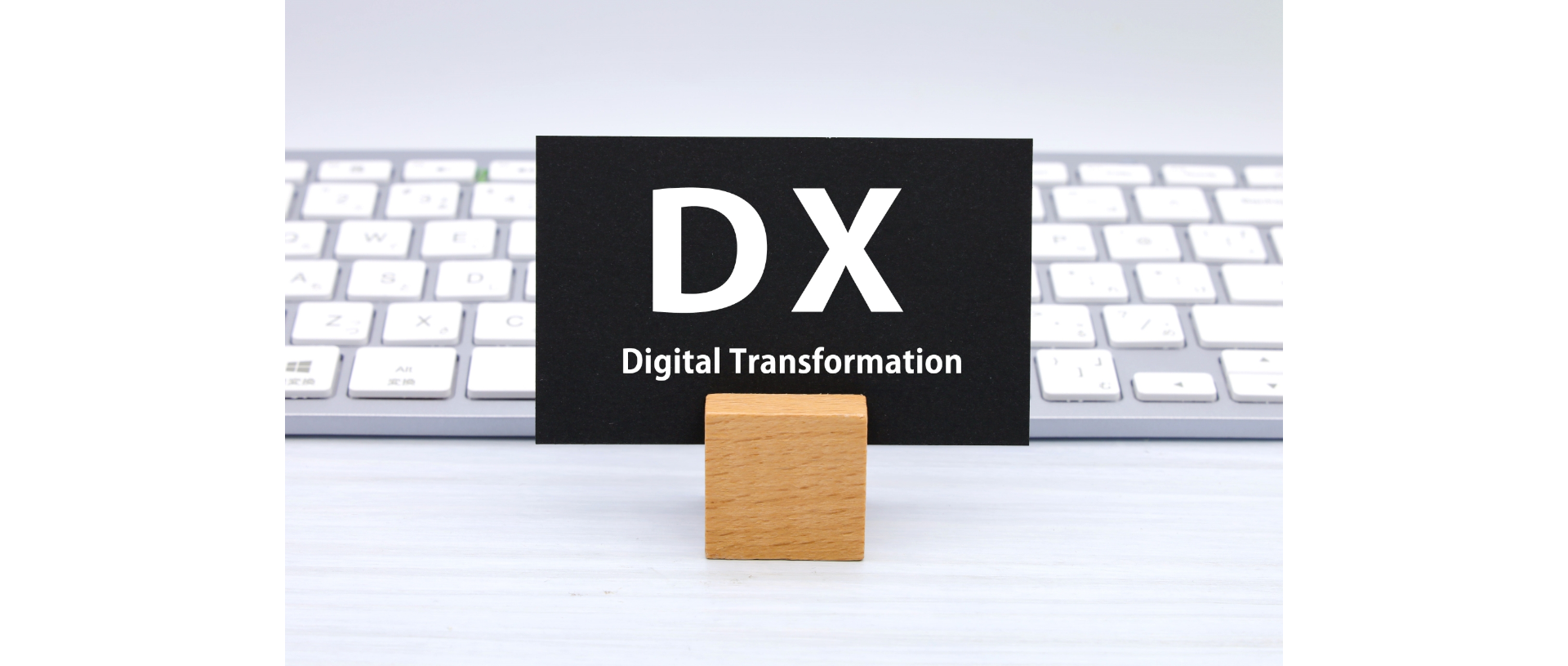
弊社はDXを支援するSFA/CRM『戦略箱ADVANCED』を提供、幅広い業種のお客様に対してDX推進のお手伝いさせていただいております。
そこで今回は製造業のお客様事例を踏まえてコラムしていきます。
そこで今回は製造業のお客様事例を踏まえてコラムしていきます。
製造業が抱える課題
業務を改善するには自社の抱える課題が何なのかを明確にする必要があります。
製造業DXを行うにあたって、そもそも製造業が抱える課題にはどのようなものがあるか再確認していきます。
しかし進捗等を共有・見える化できておらず、不透明になっているといったことはないでしょうか。
「営業の間では情報を共有できているが、営業と工場、製造現場とは共有できていない」
「リアルタイムな情報共有ができておらず、情報共有したころには手遅れだった」といった事態もあります。
今後も高齢化や人材不足が深刻化していく中で、ノウハウを継承していくことは重要です。
製造業DXを行うにあたって、そもそも製造業が抱える課題にはどのようなものがあるか再確認していきます。
・工場の製造工程・進捗管理が不透明
製造工程の進捗は生産量や納期に直結する重要な要素です。しかし進捗等を共有・見える化できておらず、不透明になっているといったことはないでしょうか。
・部門間での情報共有ができていない
製造業に限らず、部門間の情報共有は企業の重要な課題の1つです。「営業の間では情報を共有できているが、営業と工場、製造現場とは共有できていない」
「リアルタイムな情報共有ができておらず、情報共有したころには手遅れだった」といった事態もあります。
・ノウハウが継承できていない
高齢化や若手人材の不足といった課題から技術や知識の引継ぎができていないといった課題はありませんでしょうか。今後も高齢化や人材不足が深刻化していく中で、ノウハウを継承していくことは重要です。
改善例
それでは製造業が抱える課題をどのように解決していけば良いのでしょうか。
解決するためには4つの方法があると思います。
プロセスを可視化することで時間がかかっている作業を特定、業務の効率化を図ることが可能です。
情報を共有するためにチャットツール等を利用したり、進捗管理が必要な場合は部署をまたいでアクセス・確認できるツールを導入する必要があります。
用途にあったツールの導入を考えられると良いでしょう。
またツールを導入するだけではなく、社内ルールを制定または見直しすることも必要です。
蓄積した情報はは関係部門にも共有され標準化します。
そうすることでこれまで当たり前と思っていた引継ぎのMTGを行ったり、書類をさがしたりといった間接業務が効率化され会社全体でのコスト削減が図れます。
また技術の継承についてはAIを利用した映像解析ツールなどを用いることで標準化することが可能です。
そのため現在の業務にとって不要な機能や合致しないものもあるでしょう。
しかしシステムを入れ替えたり、改修することは難しいこともあると思います。
そんなときには外部ツールとの連携で作業の手間を少なくし、業務の効率化を図ります。
解決するためには4つの方法があると思います。
・進捗プロセスの可視化
進捗が共有できていない課題を解決するには進捗プロセスを可視化することが大切です。プロセスを可視化することで時間がかかっている作業を特定、業務の効率化を図ることが可能です。
・部署間で連携を行う
部署を跨いだ情報共有を行うためにはコミュニケーションツールを導入すると良いでしょう。情報を共有するためにチャットツール等を利用したり、進捗管理が必要な場合は部署をまたいでアクセス・確認できるツールを導入する必要があります。
用途にあったツールの導入を考えられると良いでしょう。
またツールを導入するだけではなく、社内ルールを制定または見直しすることも必要です。
・情報を一元管理する
情報を一元管理することで顧客とサプライヤーの情報や製造のプロセス、指示書等が蓄積されます。蓄積した情報はは関係部門にも共有され標準化します。
そうすることでこれまで当たり前と思っていた引継ぎのMTGを行ったり、書類をさがしたりといった間接業務が効率化され会社全体でのコスト削減が図れます。
また技術の継承についてはAIを利用した映像解析ツールなどを用いることで標準化することが可能です。
・基幹システムと外部ツールの連携
製造業の中には独自の古いシステムを導入している企業も珍しくありません。そのため現在の業務にとって不要な機能や合致しないものもあるでしょう。
しかしシステムを入れ替えたり、改修することは難しいこともあると思います。
そんなときには外部ツールとの連携で作業の手間を少なくし、業務の効率化を図ります。
ツールを用いた業務改善の流れ
業務を改善するには下記のような流れで取り組むと良いでしょう。
自社の課題は何か、どういったことをできるようになりたいのかを洗い出すことが大切です。
しかし課題を洗い出しても、どのように解決するのか分からない場合もあると思います。
そんなときには導入サポートを行ってる企業に相談をすることで、課題をどのように解決できるのか提案してもらいましょう。
既存のやり方から新規のやり方に変更する際には、負担が出てきます。
実際に改善されているかどうかを数値で確認することで、変化を実感することが大切です。
また改善されていない場合には新たな施策を考える必要が出てくるでしょう。
導入サポートとして導入後の運用状況をもとに改善や提案を行ってもらえるようなツール提供事業者を選ぶことも大切です。
1.現状把握・課題の特定
まずは課題を特定する必要があります。自社の課題は何か、どういったことをできるようになりたいのかを洗い出すことが大切です。
2.改善策の決定・ツールの選定
次に洗い出した課題をどのように改善するのか、導入するツールを比較検討していきます。しかし課題を洗い出しても、どのように解決するのか分からない場合もあると思います。
そんなときには導入サポートを行ってる企業に相談をすることで、課題をどのように解決できるのか提案してもらいましょう。
3.改善の実施と再評価
改善策を実施したら、実施前と後での変化を評価すると良いでしょう。既存のやり方から新規のやり方に変更する際には、負担が出てきます。
実際に改善されているかどうかを数値で確認することで、変化を実感することが大切です。
また改善されていない場合には新たな施策を考える必要が出てくるでしょう。
導入サポートとして導入後の運用状況をもとに改善や提案を行ってもらえるようなツール提供事業者を選ぶことも大切です。
まとめ
いかがでしたでしょうか。
今回のショートコラムでは製造業での課題と改善例についてご紹介させていただきました。
製造業DXで自社に最適な運用方法の決定、ツールの導入により、業務の効率化、課題解決していただけると幸いです。
今回のショートコラムでは製造業での課題と改善例についてご紹介させていただきました。
製造業DXで自社に最適な運用方法の決定、ツールの導入により、業務の効率化、課題解決していただけると幸いです。